How IoT Can Help Tools Manufacturing Companies?
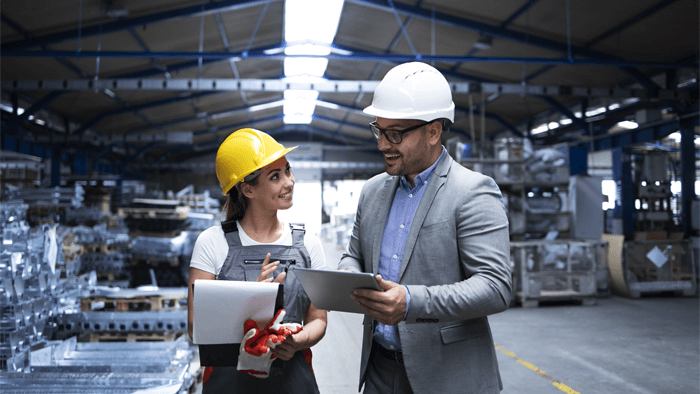
In what is referred to as the “Internet of Things,” the physical realm is turning into an information system with the actuators and sensors embedded in objects and linked through either wired or wireless internet connection.
In the industrial field, there exists a vast potential for physical systems to increase productivity in supply chain and manufacturing.
Imagine processes that can govern themselves, where smart tools can take automatic corrective actions for avoiding damages, and if any damage occurs, the individual parts can replenish themselves on their own.
These technologies have already surfaced and could drive what many in the industrial world are calling “the 4th industrial revolution” following the first steam engine, second electricity and the third information technology and automated systems.
Often when we hear about IoT’s fourth industrial revolution, we find people talking about its widespread applications in the commercial sector, business world or logistics, but nobody gives a clear example of how it can be used in a particular scenario.
Well, we shall, therefore, talk about something different for a change as we’ll highlight the potential of the internet of things (IoT) in transforming tool manufacturing companies.
Opportunities for IoT
We can categorize them into two categories:
- IoT to support the process
- IoT to support the product.
For methods that are IoT-supported, by 2020, about fifty-percent of all operations at the corporate level will adopt automated protocols of data acquisition while a quarter of these processes will possess capabilities of self-correction.
For IoT-supported products, manufacturing companies will see their revenue getting doubled in total industry share because of the internet of things and interconnected products by 2020.
Tool manufacturing companies can adopt IoT in their processes to optimize operations, lower costs, improve productivity, reduce consumption of resources, control supply chain and improve customer services.
Similarly, IoT can also provide benefits related to tool production such as increase uptime, enhance the quality of tools and use actual data from performance to drive design change in the future for the next generation of machines.
Since the internet of things provides a foundation for the automated acquisition of data, tool manufacturers can adapt their tools and processes not just to derive incremental enhancements, but also to transform their service, products, and business model.
IoT allows manufacturers to develop intelligent machines that can learn, sense and predict the needs of customers and connect with other devices in an interconnected ecosystem.
IoT to Meet Unique Requirements of Tool Manufacturers
Within tool manufacturing, several use cases reflect the increasing demand of IoT to enhance the business operations. Read further to understand the disruptive use-cases of IoT for tool manufacturers.
1. Connected Tools and IoT
From a service point of view, there are significant opportunities for tool manufacturers to use relevant tools and IoT, starting with optimizing service delivery. On the field, services based on actual performance data can enable manufacturers and service providers to improve the satisfaction of the customers and reduce the time taken to address the issue.
Monitoring conditions and remote diagnostic of connected tools can improve customer relationship, increase their satisfaction and enable manufacturers to maintain quality standards throughout the tool life cycle, for example, informing about better designs in future.
With IoT, tool manufacturers can provide innovative services like ongoing maintenance and assisted operations. The significant benefits that can result from the connected tools in the future are:
Documenting the actual performance of the machine, creating detection and early warning signals, and establishing closed-loop control that could drive significant quality enhancements in future devices.
Making the transition into new services easier that could bring significantly higher margins and increase customer satisfaction.
2. Supply Chain Connection and IoT
The modern supply chain has witnessed a substantial change since it adopted mobile devices and a variety of other sensors, including GPS and RFID, for keeping better track of inventory and goods in warehouses and transit. But even though the performance of the supply chain has improved, there still exist several gaps that must be filled.
Customers always demand better service from tool manufactures. The most important demand of the customers is the faster time of delivery. The network of micro logistics can accelerate the delivery of products to the customers.
For reducing lead time of orders, many tool manufacturers are looking to shift from traditional large centers and explore local smaller warehouses for a viable micro logistics network.
The process is not simple, and for implementing a network like this, tool manufacturing companies need to bring greater visibility in their logistics and inventory for preventing costs from getting out of hands. IoT gives tool manufacturers an opportunity to re-examine their expectations from RFID sensors and see their dreams turn into a reality.
In the interconnected supply chain, the use of the IoT may initially be directed at asset management (e.g., trucks, shipping containers, and pallets). It depends upon simplified, low-cost data acquisition for enabling some critical decision which must be made by tool manufacturers in managing the supply chain.
In simple words, for supply chain management, tool manufacturing companies can use the internet of things for creating specific visibility that is important for ordinary business objects, such as inventory position, orders, and shipments.
Moreover, IoT can help tool manufacturers monitor data in real time which would allow them to recognize changes or issues and respond to them more efficiently.
The significant benefits that can be acquired from an interconnected supply chain in tool manufacturing business are:
- Better management of inventory position in a complex network of logistics with more visibility of inventory.
- Increased capabilities for fulfilling execution through more localized, smaller warehouses that are at a lesser distance from customers.
3. Smart Manufacturing and IoT
The industry dynamics and the global market is pushing tool manufacturing companies into rethinking their operations, and efficient factory management has become essential.
In smart manufacturing, data analytics from IoT is required for increasing efficiency and improving utilization of assets.
If old and new data is combined with analytics-generated information, it will give workers certain flexibility and capability of decision-making required to handle demand variability and increasing complexity of the market.
Many plant workers in tool manufacturing companies are weighed down by handling large volumes of data and struggle in understanding what the data represents. In a smart manufacturing system, it is essential to have a layer of intelligence that connects the plant with the enterprise to provide real-time data for decision-making.
In tool manufacturing plants, an intelligent platform developed through IoT can connect real-time data coming from the plant machines with business intelligence to administer the enterprise decisions.
An immediate gain from this “internet of assets” is that it would eliminate the need for a worker to enter and acquire data from the plant. In the long-term, such systems can provide autonomous operations or self-healing. Eventually, IoT will make tool manufacturers operationally intelligent to look across materials, tools and other information.
Other benefits that will result from adopting smart manufacturing are:
- Increasing quality and reliability with access to operating intelligence.
- Connecting plant-level decisions with enterprise-level objectives to allow real-time decision making.
Building industrial IoT software solutions for the manufacturing industry can help improve decision-making processes.
4. Predictive Maintenance with IoT
Real-time status monitoring is not the only benefit of IoT smart manufacturing system, but it can also be used to reduce machine failures through predictive maintenance. Traditionally, machine maintenance involves following routine preventative maintenance.
It generally includes replacing components of the machine based on the suggested timeline of the manufacturer rather than actual data from the device itself.
Since tool manufacturing companies have complex machines and parts, it means that they’ll be paying substantial amounts for unnecessary replacement parts or scheduled preventative maintenance which, in most cases, is not required.
Or, if something goes wrong during scheduled maintenance, they might have to suffer from unexpected downtime which means a halt of production and loss of profits.
Predictive maintenance removes the guesswork as decisions for support can be based on the data provided by the machine in real time. For example, temperature sensors and vibration sensors wirelessly connected with the device can sense any signs of loose, misaligned or worn out parts.
The information can then be transmitted to a controller that makes the information available to the technicians immediately so that repairs can be made.
By real-time monitoring of machine components for increasing temperature and vibration, issues can be identified and resolved before they become worse and cause more damage or unexpected downtime. With time, the data from the machine creates a performance log which can be used for making better maintenance decisions in the future.
IoT can Streamline Communications in Factory
For tool manufacturing companies, IoT is not just useful for improving machine operations. In fact, IoT can also enable better interaction between human workers and have a significant impact on tool production lines.
For example, in a manual system, a machine worker may have to walk to the technical manager to get help with a particular issue. On the other hand, if the system is made wireless through IoT, switches, tower lights and pushbuttons can be used for alerting managers whenever assistance is required.
Think of a wireless notification system through which a worker can press a button or switch to notify the technician or manager that he requires assistance with a particular machine.
A light connected to the device would then show the technician or manager where aid is needed. Colors can also be assigned to the lights to indicate if a manager (red) is required or a technician (yellow) is required.
Wireless pushbuttons with LEDs can aid two-way communication if LEDs are configured to change colors when the technician or manager indicates that he is coming to solve the issue.
Use of wireless notifications means that manager and technicians would no longer have to continuously check each machine and workers won’t have to go to them physically when assistance is required. With an interconnected network of devices streamlining communications, technicians, managers, and workers can use their time more productively and efficiently.
What the Future Holds
IoT can genuinely transform the way tool manufacturing businesses work, but specific challenges are being faced in its implementation. In tool manufacturing machinery, it is critical to receive the message and traverse that message promptly to handle the machines.
Sometimes the devices are located at considerable distances from the asset and in such a case, timely communication becomes crucial to utilize the full potential of IoT.
IoT needs upgrades and expansions to meet the rapidly changing industrial requirements. Tool manufacturers must build their smart manufacturing IoT systems with flexible software and hardware that can adopt evolving technological developments.
An IoT-equipped manufacturing unit can communicate with machines and self-heal. However, data which is collected from such groups must be analyzed for improving the production, efficiency, and profits. With more intelligent and flexible manufacturing, optimization of logistics for tool manufacturers leads to sustainable and better operations and quality control.
Tool manufacturing companies must overcome many hurdles in implementing IoT if they wish to avail of its full advantages.
In the coming years, IT departments will face several challenges to managing the complex data as the new systems that are to be switched to IoT will require sophisticated algorithms and data management techniques.
The potential problems for IoT can be overcome through a solution that would monitor the whole information technology and data created by the machine.
The IoT systems will also require advanced monitoring protocols and security systems to avoid potential threats of the security breach.
All in all, a lot of efforts needs to be made before IoT can be implemented in a tool manufacturing business, but once the system becomes operational, there will be no stopping it.
To get an in-depth understanding of how IoT can work in manufacturing companies, get in touch with our team of IoT application development experts.
Start a conversation by filling the form
All information will be kept confidential.